Atlantic Copper, May 2017 - Present
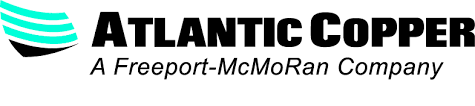
Developing improvements for Sulphuric Acid Plants, Process Engineer is a key rol in the company, analyzing the necesities of operation, engineering or maintenance teams, coordinating the action between departments and coordinating improvements with the rest of the areas in the plant.
Graphic Summary
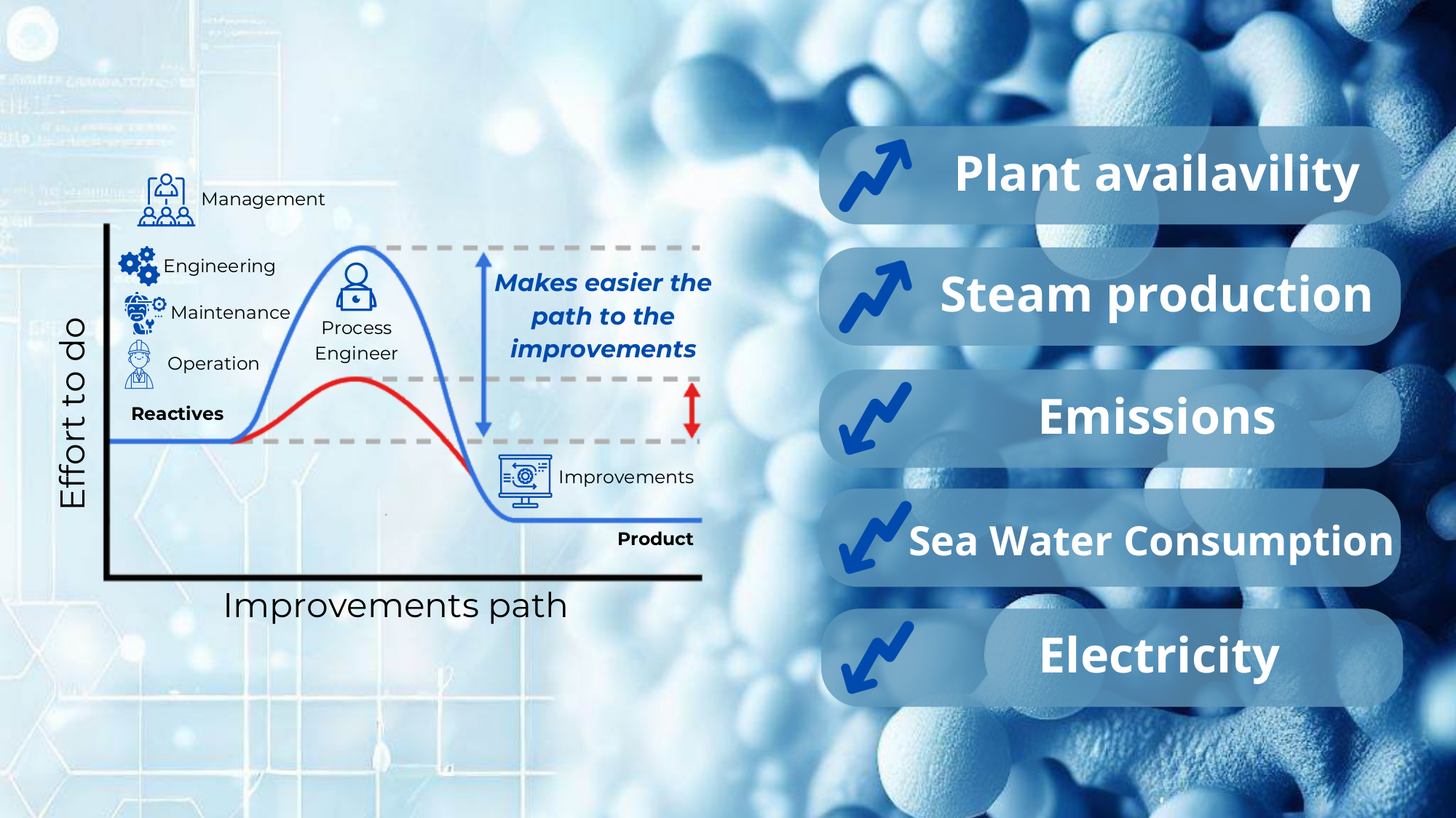
Experience Highlights
Steam Gas Reduction System (2024/2026): Project Manager for developing and executing a modification of the refinery furnaces in order to reduce gas natural consumption during the anode copper final reduction process (6MMeuros).
Gypsum plant capacity improvements (2023): Gypsum plant is the downstream of sulphuric acid productions. Its goal is converted dilute acid into a gypsum subproduct. However, capacity and availability problems in the gypsum plant could produce the shutdown of the whole facility. Applying 6 sigma methodology, the root cause of the capacity limitation was found. The new operational point was applied and capacity was increase from 58% to more than 80%.
Acid Quality Management (2022): In order to manage one of the sulphuric acid impurities, oxygen peroxide is added. Excessive feeding of this additive results in another quality measure exceeding its specified limits. Six sigma methodology was applied to solve this problem. Root cause was found and some changes was recommended to the operation team. After two years of the new operation, no quality problems have been reported.
Shift Manager (General shutdown 2024 | General shutdown 2022 | General shutdown 2019): Catalyst replacement activities (30 workers)
Minor elements Management (2021-*): Responsible of bottleneck analysis in order to increase element "A" removal without affecting the facility integrity. Follow-up of important minor elements behavior. Responsible for analyzing the behavior of minor element "B" in the process, detecting the influence variables and making easier the planning of the feed mixture. Increase the minor element treatment in the copper raw material without affecting the plant integrity or the product and subproduct quality gives an important business edge.
Energy Management System (2020-*): Energy Team Responsible in Sulphuric Acid Plant and Effluent Treatment plant. 30% reduction in the refrigeration water requirement. 10% reduction in the main blower consumption. Steam production increased. Projects proposed to potential recovering about 200 GWh/year
Sulphuric Acid Plant 1 Heat Recovery System HAZOP staff (2020)
Machine Learning models (2020-*): Catalyst pressure drop behavior prediction model, saving more than 20 days of production. Gas management optimization model which help team to minimize electrical consumption and maximize steam production. Gas Cleaning plant capacity follow-up which let the operator knows their gas management capacity. SO2 emission follow-up which help the team to detect changes in the process as soon as they happened. Catalyst activity follow-up which help to understand the performance of the catalyst without manual analysis.
Focus Group (2019-2021): Project focused on increasing the proactivity of the workers regarding safety issues. Consists of a multidisciplinary team that meet themselves periodically to analyze the most important risks in each area, developing solutions for each one and sharing them with the rest of the organization.
Sulphuric Acid Plant 3 HAZOP staff (2019)
Emission Reduction Plan (2018-2022): Strategic project to decrease emissions level in the whole facility. Developing a new catalyst distribution for Sulphuric Acid Plant (SAP) 2 (Emission level potencial reduction of 20%). Pipe modification in SAP3 and SAP 1 to avoid gases leakage (Emission level was reduced in 15% per plant). Developing weekly follow up with operation and maintenance departments for faster troubleshooting.
Gas Management (2019-*): Atmospheric air intake is an important source of emission increase and production losses. Detecting the point of the air inlet allow maintenance team to be focused on the correct location. Developing a real time model for detecting points of air inlets makes faster maintenance answer. In the other hand, avoiding air intakes saves energy consumption.
Acid Quality (2017): Acid quality depends on the level of certain minor element. The knowledge about the characterization of one of these minor elements is very important to select the correct technology for remove it. Some tests were developed to demonstrate that the current characterization of this element in this plant is different than the standard and the selected technology was not the best one, saving about 2MM€.